
Unique Features
Thinking differently.
Updated 3/30/2020
The
GC&W layout project was intended to be different from the
start. While 50 years of model railroading was certainly a
factor, more important were the experiences gained in a lifetime
of home remodeling and the location opportunities available in
an area with low cost-of-living. Adding to the fun were advances
in technology and materials.
The Building and Location
An entire standalone building dedicated to a personal model
railroad layout and support is relatively unique. In our case,
we had the opportunity to purchase a "well-loved" post-frame
building (locally known as a "pole barn") and lot, for less than
new construction at our basement-less home. Added bonus was the
building's location only 150 feet away from the combined
mainlines of three Class I railroads.
The 66' by 45' structure initially promised to be beyond huge by
N scale standards, but reality dictated space for support
tasks and “necessities”... such as a restroom... and
we lost 26' in the long dimension. Early planning put some of
the support on a partial second floor (“mezzanine”), but that
was deemed impractical.
As with any bargain real estate acquisition, the building needed
a lot of work, starting with replacing the roof. The façade was
also replaced, adding a portico for aesthetics and to control
morning heat in the summer. All wiring including the utility
feed was replaced and relocated, HVAC replaced, two restrooms
became one, the vestigial kitchen was gutted and converted into
an art studio, and the concrete main floor was leveled to fix
make-do additions accreted over decades. The original attic,
previously used for storage, was cut back to create a 13' high
ceiling in what was to be the layout area.
Layout
Foundation
XPS foam and steel are not your father's benchwork. Many
years of operating and maintaining model train displays grew
into hard lessons in layout construction and what not to do.
Number One on the “don't!” hit parade was wood framing and
work surfaces in environments subject to extremes in humidity
and temperature. Southern Illinois is given to very humid
summers and nearly desert-dry winters; even a well-engineered
HVAC system struggles against the outdoor ambient to contain
the extremes. So, no wood if possible.
“XPS” is shorthand for “extruded polystyrene”. The
Owens-Corning version of XPS insulation panels, “Foamular”, is
popularly known as “pink foam”, sold by national and large
regional home improvement stores. It is very lightweight, easy
to handle, and easy to work with hand and power tools,
although the sawdust can be messy since it is static-charged
and sticks to everything. Thicker sizes such as the 2"
used on the layout are rigid enough to use directly on
framework without additional backing. Foam-safe adhesives are
required since normal solvent-based construction glues
dissolve XPS foam; Gorilla™ Construction Adhesive was used to
adhere the foam topper to the steel benchwork.
A notable disadvantage of XPS foam construction is it will not
reliably hold screws or nails. There are foam-specific
augur-type screw anchors similar to drywall anchors, but these
are expensive. The fastening system to use with foam is modern
adhesives.
You may or may not have heard of steel studs. These are metal
channels shaped into the dimensions of common wood framing
lumber such as 2x4s and 2x6s. They are popular in commercial
construction, even required by code in many areas, most
obviously because they are fireproof. 2x4-equivalent studs and
“rails”, the channels the studs slide into, form the basic
layout frame, and 2x2-sized studs and rails are formed into
the box beams seen in the photo above, used as simple trusses
in supporting the around-the-wall portions of the layout. Cutting metal studs to size is not
as daunting as it may seem since metal-cutting circular saw
blades have been available to the trades for several years,
and now can be found in most home improvement stores. While
it is common to use self-drilling screws with metal studs,
most of the steel construction on the layout is held
together with “pop” rivets.
High
Ceilings and Exhibit-Grade Lighting
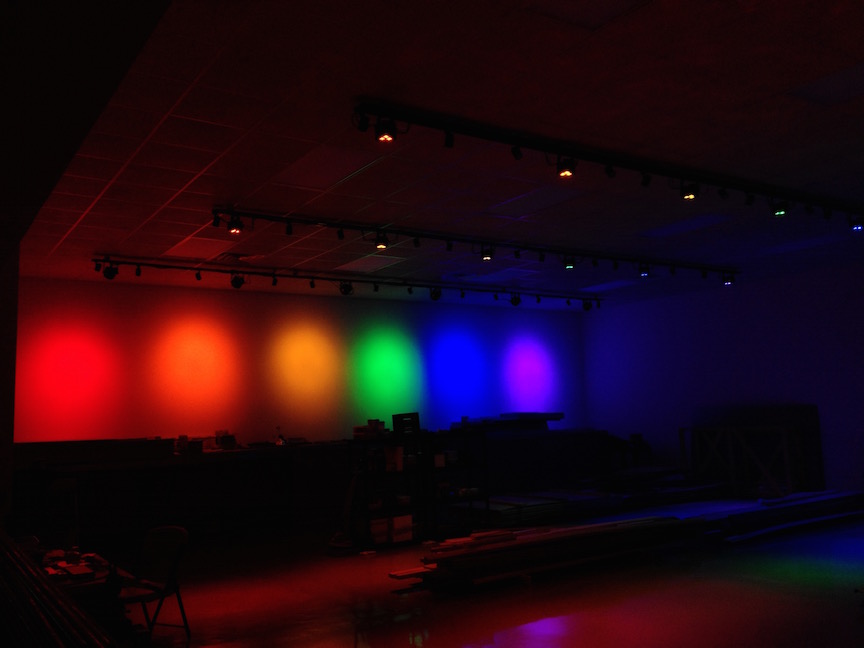
Wide-open
spaces are a personal bias, so the opportunity of a large barn
with no columns and a high overhead structure was a natural
for a really big room for the trains. Visits to the Colorado Model Railroad Museum's display
layout in Greeley, Colorado, reinforced the concept of a
large open space with high ceilings as an excellent stage for
big layout development.
One challenge, however – high ceilings come with added work in
lighting design. Special-effects lighting was part of the
overall plan, including daylight, sunset/sunrise and night
ambience, and possibly a stormy pall over the layout. Key
objective here was all lighting was to be LED. Effective
large-space LED lighting was prohibitively expensive during
the early phases of construction, but prices fortunately
dropped quickly enough to use LED troffers in the drop ceiling
for general room lighting.
Research into special effects lighting started with the
then-new technology of wireless-controlled color-changing
light bulbs marketed to early-adopter consumers. The reality
was disappointing: the bulbs were expensive, not very bright,
and they had a limited palette of colors. Especially a problem
was the number of bulbs controllable by the hub, constrained
to maybe a quarter of what was needed for the full system, and
multiple hubs in the same space were not supported due to
network protocol limitations.
So scratch that idea. Even though there are now many more
choices, improved color control and lower costs than when we
started, and the limitations and complexities are different,
there are still weaknesses that make the consumer-grade
programmable color-changing lighting unsuitable for the layout
project.
LED stage lighting was becoming affordable in the interim,
with spotlights and effects lighting tailored for the DJ
market. These lower-end stage lights were tested and confirmed
as the solution. A support system of steel struts was
engineered and added to the ceiling structure, with a wired
control network using the DMX512 professional lighting
protocol. Track lighting with 5000K white spotlights was added
for better “daylight” illumination. Newer, better-performing
stage lights (“PAR cans”) are being phased in as time and
budget permit. Four banks of stage lights are
computer-controlled, with each light separately addressable
and available for lighting effects such as sunset and sunrise,
moonlit night... and sometimes the occasional thunderstorm.
The
Sky
Discussions with fellow modelers about “the best way” to
create backdrops yielded three different options: photographed
panoramas printed on a large-format inkjet printer,
fully-painted backdrops including background scenes such as
forests or hills, or the simplest, blue paint.
Photographed
panoramas were seriously considered, both commercially-sourced
and produced from our own photography such as the image to the
right of Kelso, California. Cost of either option was
well into four figures given the 140 feet of backdrop.
Large-format inkjet printing is expensive, plus we would lose
revision flexibility if a layout scene was changed and no longer
made sense against the backdrop.
Hand-painted landscape murals were briefly considered, dismissed
as too much time and effort. We devised a scheme to paint
backdrops on panels which would then allow off-wall production,
but the process of hiding the joints and blending the panels
added to the work of painting 560 square feet worth of mural.
So... blue paint, maybe add horizon
scenes later. Simple. However, the sky was supposed to look
somewhat real, and even a well-matched shade would look wrong if
monochromatic. A process of fading the blue to a lighter horizon
was devised, also gradually changing the blend to the lighter,
hazier skies of the Midwest as the layout representation moves
from west to east. Horizon scenes are to be addressed with 3D
scenery and photographic flats.
The panoramic view of the room to the right also shows the full
extent of the sky, the lighting system and also gives a sense of
the space.
The
Stars
What is a sky without stars at night? As mentioned, much
consideration was given to the possibility of special effects
for nighttime operations. After a fair amount of research and
still under development, a scheme using special
ultraviolet-sensitive “invisible” paint from the theater staging
industry was devised, coupled with recent improvements in
affordable UV LEDs. At left is an early test example of a starry
night sky, the UV source we're working with currently has much
less visible purple.
Computer
Control
Another special
feature of the GC&W is layout control performed entirely
through computer interfaces. There are no toggle switches or
pushbuttons anywhere on the layout controlling power
distribution, throwing track switches, or otherwise handling
tasks traditionally assigned to manual controls. Under a JMRI
supervisor system, touchscreen pads at local control points
handle operator controls and display track conditions including
turnout positions, block occupancy and signal aspects. Shown
here to the right is the panel controlling the junction at
"O'Fallons". Communications between the supervisor computer,
touch panels and operator throttles are handled through an
enterprise-class high capacity WiFi system.
The dispatcher has the option of controlling every operating
detail of the layout on his or her dedicated computer, either in
a broad view or displaying local panels as needed.
A
Virtual Window for Local Railfanning
The original room
concept proposed a second level with an observation platform
overlooking the layout, with the added bonus of windows to
watch passing Canadian National, BNSF, and Norfolk Southern
trains 150 feet to the west of the building. As the layout
plan developed, access to the observation deck was determined
to have too high a cost in layout space. Also, adding the
windows was going to be expensive, and would have only
afforded views from the deck, anyway. Instead, a dedicated
"railcam" system was designed, using a high-resolution
professional video camera and a large LCD panel television
that could be seen from every point in the layout room.
Return to Home Page